Maximise workshop efficiency: Relief grind your cutting units
Maximise workshop efficiency: Relief grind your cutting units: Ian Robson, of ProSport UK Ltd, the UK & Ireland Importer/Distributor for Foley Company, explains why relief grinding maximises the performance of reels by giving a factory finish every time.
Avital question for a workshop manager is how to maximise efficiency and minimise labour and maintenance equipment costs. One area to achieve excellent savings is to look at how you maintain the sharpness of your cutting units.

Maximise workshop efficiency: Relief grind your cutting units
Firstly, why is having sharp cylinders (reels) that are the correct shape so important anyway? The answer is obvious – unhealthy turf brings a whole host of other issues which are costly to correct.
Therefore, prevention is a far more economic approach than a cure.
A huge amount of research and development has gone into designing a cutting unit to produce the cleanest cut possible with the least amount of fraying and tissue damage to the plant. The result is that all manufacturers of grass cutting equipment supply new units with relief ground edges.
WHY RELIEF GRIND?
Tests carried out by leading manufacturers have established that relief ground cylinders stay on cut up to 3 times longer than spun ground ones and require less horse power to drive the unit, resulting in greater fuel efficiency and less stress on the hydraulic power systems. In addition, a relief ground cylinder will withstand the abrasive effects of top dressing far better than one spun ground because the relief edge on both the bed-knife and the cylinder allows the top dressing to clear the cutting blades easily, helping to prevent the dulling effect seen on spun only units.
Continual relief grinding also decreases the squeezing and tearing of the grass as the units get dull, and most importantly it allows the cylinder to be returned to a factory specification perfect cylinder as quickly as possible.
The overall cleaner cut achieved by relief grinding gives a better after-cut appearance, increased recovery rate due to the clean cut of the grass and reduces the stress on components because less horsepower is needed to drive the cylinder.
As a reel wears flat and loses shape (becomes coned), more stress and strain is put on the cutting systems.
A 5-gang cutting unit with relief can require up to 4.5 HP (5 x 0.88HP = 4.5HP) to drive the cutting units therefore a 35HP engine has 30.5HP remaining to drive the rest of the traction system. A 5-gang unit which has been spun ground only, can require up to 13Hp (5 x 2.59HP = 13HP) leaving only 22HP to drive the rest of the traction system.
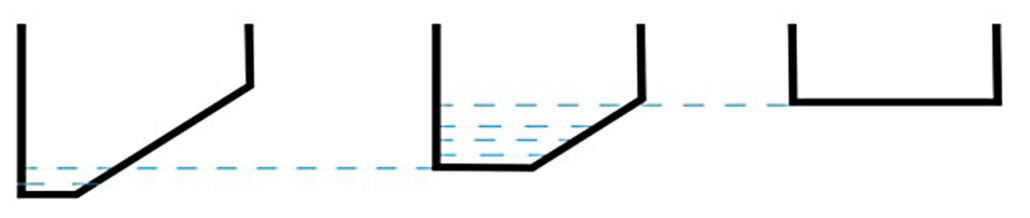
Maximise workshop efficiency: Relief grind your cutting units
So, it has been established that relief grinding your cutting units saves you money not only by reducing workshop maintenance time with far fewer grinds but also through a reduction in fuel costs and replacement parts.
It is also important to acknowledge what relief grinding does for a reel. By removing metal from the trailing edge of the blade it forms a relief angle, which reduces the contact area of the cutting edges, resulting in less friction, longer wear life.
Typically, when a new mower is delivered the reels will be a perfect cylindrical shape. Over time the blade naturally loses shape, and the sharp edge it arrives with becomes flat and dull, often meaning the reel is no longer a perfect cylinder from end to end. This is referred to as ‘coning’ and a natural point for grinding to take place. The decision then sits between touch-up and spin grinding, or relief grinding.
If there is sufficient relief still on the reel then a quick touch-up is fine but once more than 50% of the relief has gone my advice would be to relief grind again and remove any coning. Failure to remove the coning will eventually be seen in an uneven cut appearance of your turf.
Foley machines are set-up for both choices, and some models, such as the ACCU-Sharp, ACCU-Pro and ACCU-Master, have automatic grinding pre-sets and adjustment systems to decrease time and labour.
But, the main question mentioned at the beginning comes back; how to get the most out of your workshop resources by choosing the most effective method to sharpen your cutting units. The answer is to trust the manufacturer’s judgement and return the reels as close to the original factory standard as possible, and for that, relief grinding is the best option. The bonus is this method also maximises performance and gives the best cut.