JCB’s Joe helps NHS
JCB’s Joe helps NHS: JCB and a team of volunteer employees have set up mini production lines to come to the aid of the nation’s NHS heroes in need of personal protective equipment.
Principal Electronics Engineer and father-of-two James Morley – who is normally based at JCB’s World HQ in Rocester – has converted the garage at his Derbyshire home to produce vital supplies.
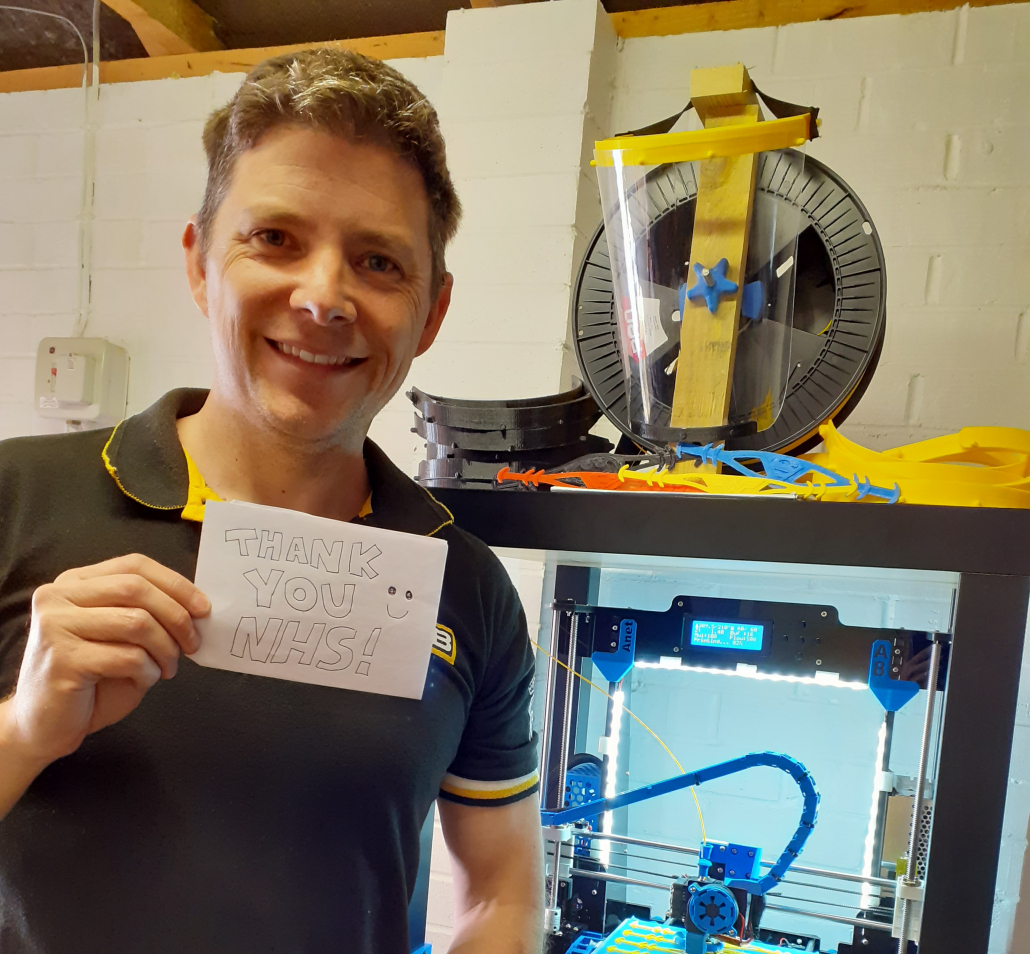
JCB’s Joe helps NHS
And inspired by his efforts, JCB has re-opened its Innovation Centre at the World HQ so colleagues and Tooling and Moulding Engineers Joe Mumby, 22, and Joe Bagley, 25, of Ashby de-la-Zouch can also volunteer and have free use of the company’s 3D rapid prototype machines to help produce medical grade visors for NHS staff. The World HQ and JCB’s other UK manufacturing plants fell silent last month as a result of the disruption caused by the Coronavirus and the vast majority of employees furloughed.
For Joe Mumby, of Hilton, Derbyshire, volunteering to produce the vital NHS kit has also taken on a poignant significance as he and his family come to terms with the death of his father’s cousin from Coronavirus in the past few days.
Joe said: “Helping with the production of visors is the least I could do as this is a very testing time for everyone, including my own family. It’s fantastic that JCB has given us the opportunity to give something back to those who are the front line of the virus in what must be a very scary time for them.”
So far, the volunteer production line set up at JCB has produced 50 visors for distribution to surgeries in the Rocester and Uttoxeter area with the help of material donated by the JCB Academy.
With the visor material now exhausted, Joe and Joe are concentrating their efforts on producing hundreds of head bands required for the visors before despatching them to a Warwickshire company for final assembly.
Meanwhile James Morley, 43, who was the original inspiration for the project, has transformed his rapid prototyping machine in the garage of his home in Belper, near Derby from making toys for children Alice, eight and Joshua, five, to producing NHS kit.
Having made 20 visors, he is now diversifying his domestic production line to make components, which convert snorkelling masks for use with hospital ventilators. He is also rapid prototyping so-called ‘superhero nurse’ headbands which make face masks more comfortable for medical staff to wear as they fit on the back of the head rather than on to the back of ears.
James says he has been touched by the generosity of people during his voluntary work – including the donation of half a kilometre of plastic for his project from one well-wisher.
He said: “While browsing social media on the state of the Covid-19 situation, I was aware that there was a huge shortage of medical grade personal protective equipment for our NHS and other healthcare communities around the UK. It made me dust off my 3D printer and help contribute to the fight against Covid-19 and support our heroic NHS.
“I am glad I can help out and make use of my printer during this national crisis and keep myself active with volunteers during the furlough period. It is amazing what support there is out there and how much people would like to help.”
JCB Chief Innovation Officer Tim Burnhope said: “JCB is delighted to be able to play a role in helping provide the fantastic NHS with protective equipment. The volunteer employees who are part of this amazing effort are also to be commended for stepping up at this time of national crisis.”
3D printers take Computer Aided Design data and build it into a 3D object using very fine layers of melted plastic. The plastic is heated up to around 210°C and then extruded on to a flat metal plate, that is also heated up to around 60°C. Over the next few hours, the printer will finish the object before it is simply peeled off the flat plate and used.
For the latest industry news visit turfmatters.co.uk/news
Get all of the big headlines, pictures, opinions and videos on stories that matter to you.
Follow us on Twitter and Instagram for fun, fresh and engaging content.
You can also find us on Facebook for more of your must-see news, features, videos and pictures from Turf Matters.